Decreasing Cost of Inventory Accuracy
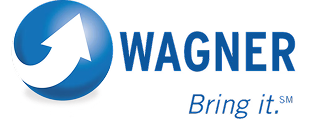
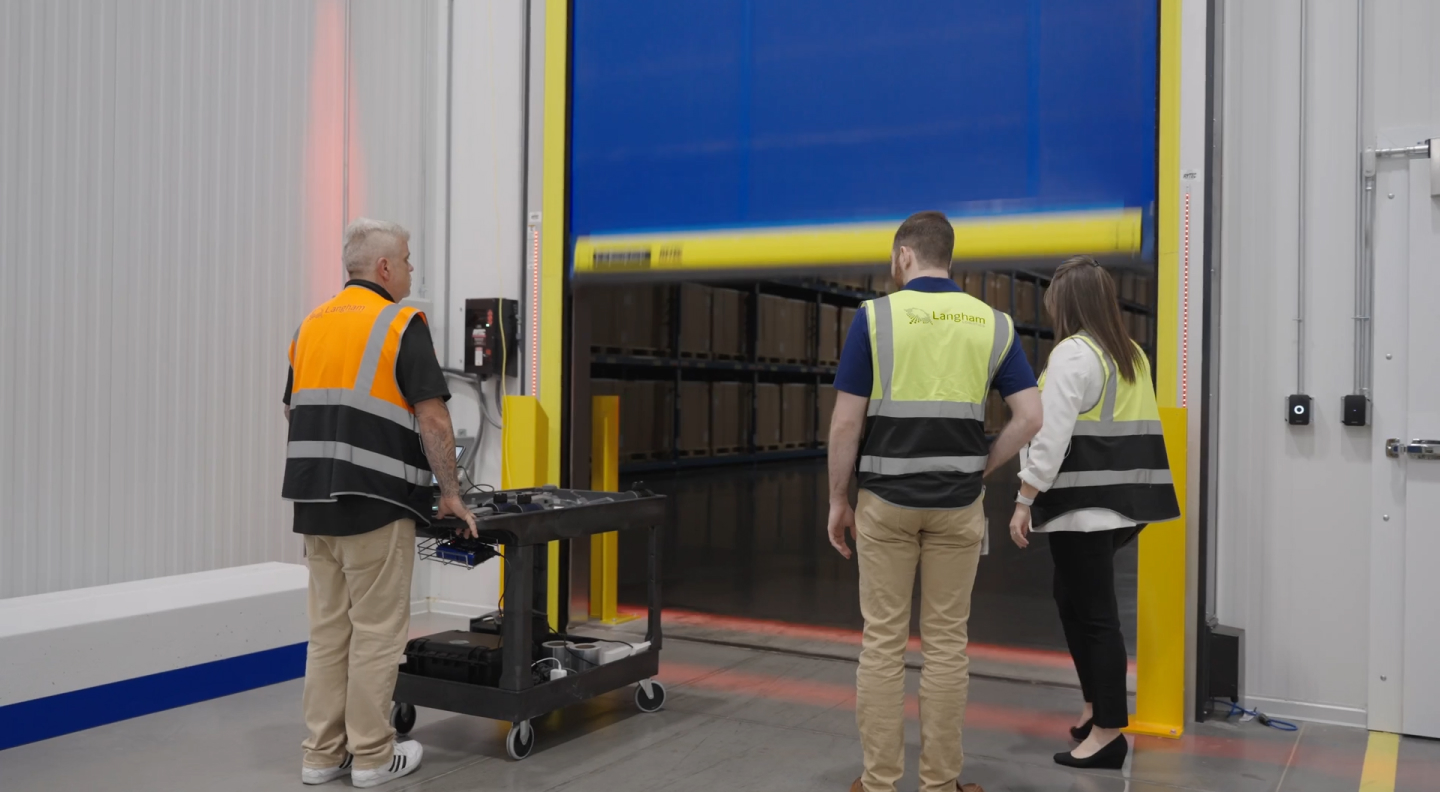
Challenge
Based in North Kansas City, Missouri, Wagner Logistics (Wagner) specializes in contract warehousing and transportation across 31 U.S. markets. The facility in Monroe, North Louisiana is the largest and handles just under a ½ million pallets per year. The Monroe team experienced a limited labor market and needed to better utilize their existing staff. They wanted to free workers, especially inventory control specialists, from repetitive inventory monitoring so they could focus on more value-added tasks and improve operations throughout the warehouse. Executing this was a challenge given the large inventory volume.
Solution
Wagner turned to Gather AI to integrate a drone-powered inventory monitoring solution in their warehouse to help solve these challenges. Gather AI’s software enables drones to fly autonomously through warehouses with no GPS or WiFi to photograph inventory stored in pallet locations. The AI reads bar codes, text, and other information in the photographs and automatically compares it with what’s in the warehouse management system (WMS). The warehouse manager can view inventory data in real-time from a web dashboard and easily identify and fix inventory exceptions, even creating a to-do list for their team.
Results
Prior to working with Gather AI, taking a full inventory of 45,000 rack locations took six to eight weeks, but with Gather AI, they were able to complete it in half the time with fewer people. Robin Romero, Wagner Industrial Engineer says, “We can only physically visit so many locations in a day, but with a drone, we're able to check locations faster and get ahead. So if we accidentally misplace a pallet, we have a much higher chance of finding it before it ages out or we need it for a shipping order. The Gather AI solution really increased the speed of finding lost product and makes the warehouse not feel so big.”
Because they can do inventory more quickly, Wagner has been able to reduce inventory errors by 50% which represents roughly a million dollars worth of product.
Additionally, the solution has also improved safety and mitigated risk as employees no longer need to go up on lifts multiple times a day. It has also helped prevent future inventory monitoring and process issues. For example, if there’s an area of the warehouse that consistently sees cycle count errors, the team can assume there may be a network issue and look into it.
Transform your warehouse.
No infrastructure changes necessary
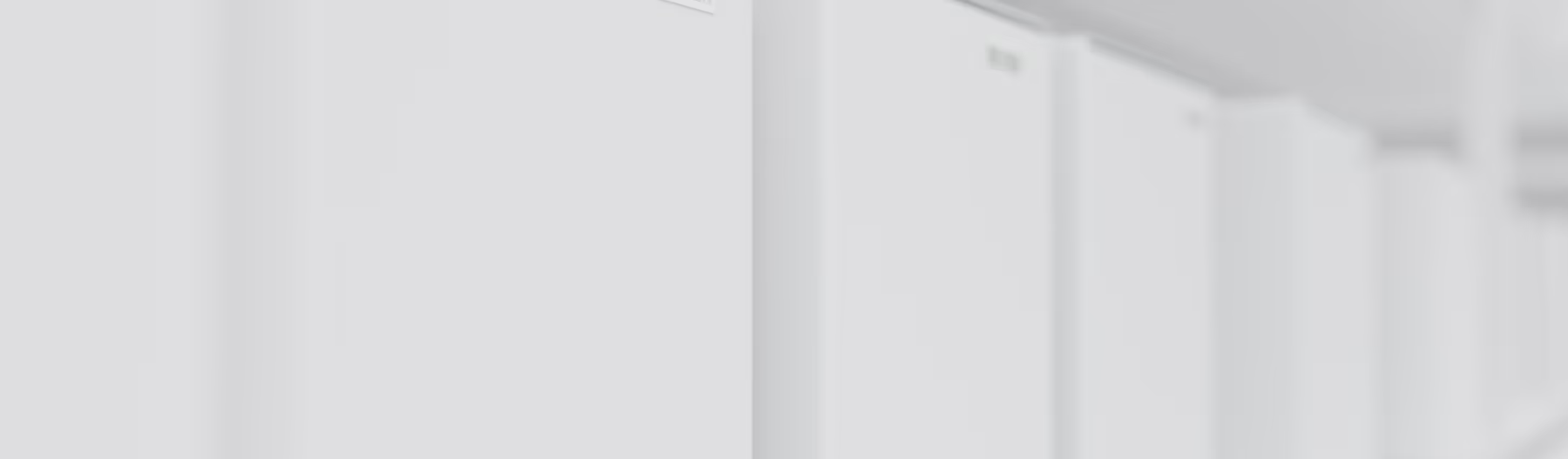