Manufacturing Technology: Autonomous Drones for Inventory Monitoring
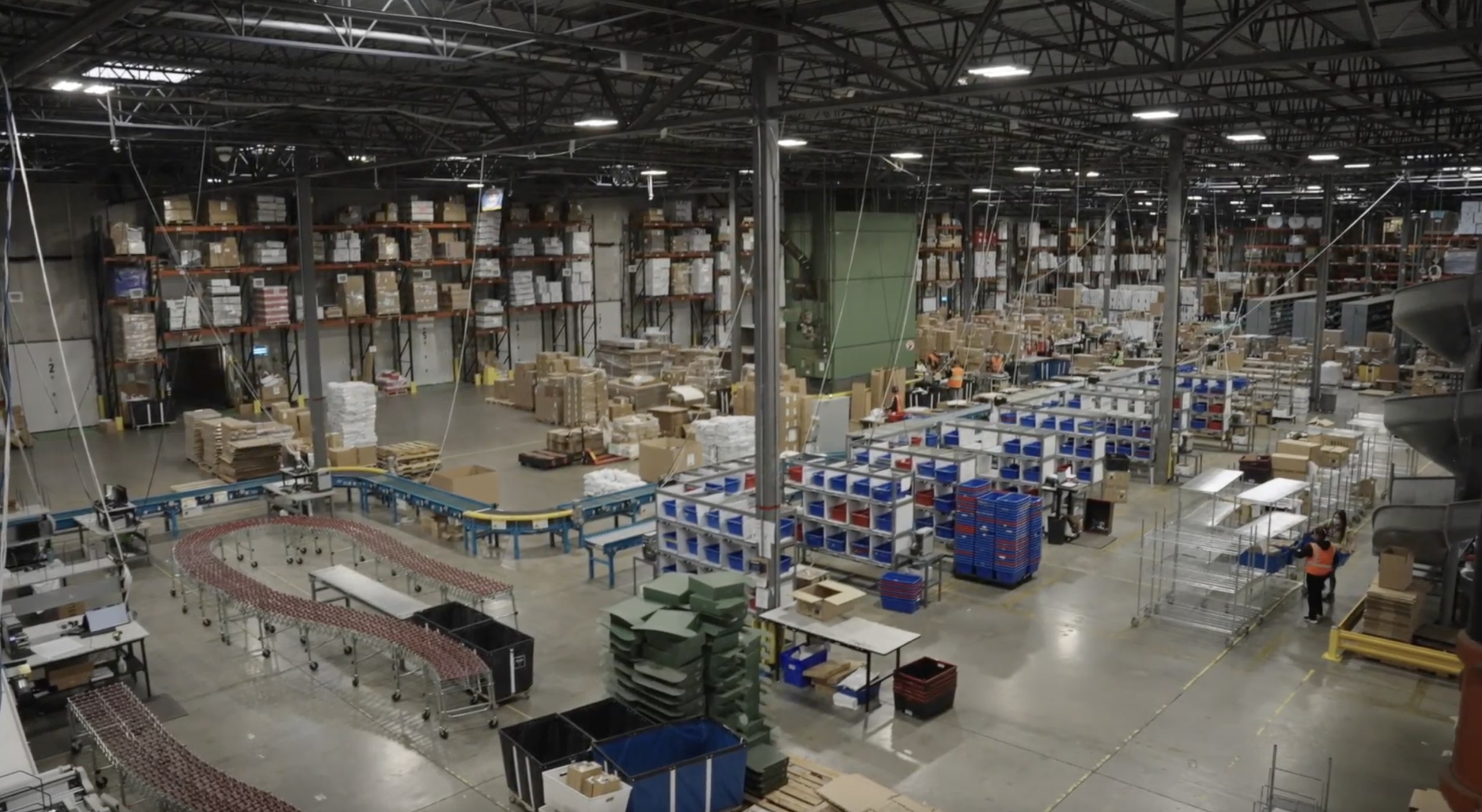
Introduction
Manufacturing supply chain teams tell us how efficient inventory management is crucial for them to maintain smooth operations and meet customer demands. Unforeseen inventory shortages lead to costly disruptions for downstream processes. For automotive manufacturers, one minute of downtime costs $22,000 or $1.3 million per hour. Additionally, the raw materials needed to get the line back up and moving may have to be expedited which can also be a significant cost.
Today, manufacturers combat low inventory accuracy by having team members cycle count and by doing regular manual full-facility inventory counts. These counts are costly in manpower and time and don’t offer the traceability and accountability needed to ensure that inventories remain accurate.
The Gather AI drone-powered inventory monitoring solution enables manufacturing facilities to eliminate inventory-related downtime. By employing autonomous drones to scan pallet locations and identify inventory exceptions, our solution enables inventory control teams to find and fix inventory errors in the Warehouse Management System (WMS), MES (Manufacturing Execution System (MES), or Enterprise Resource Planning (ERP), before they become errors that impact production.
Cost of Inventory Inaccuracy
Inaccurate inventory management poses significant challenges for manufacturing facilities. When inventory levels are discrepant, procurement teams struggle to plan and order the correct inventory, leading to disruptions in the production line. The repercussions can be severe, with the cost of downtime estimated at $22,000 per minute for automotive manufacturers. Many times parts need to be expedited from suppliers or alternative locations at a premium, incurring further expenses and delaying the resumption of production.
Additionally, once the product has been manufactured and is stored in a finished goods storage location, inaccurate inventory can mean delayed shipments, missed shipments, or, in the worst case, having to manufacture the product again. This means going into the system, creating a work order, and making another product to meet demand.
Current Practices
Traditionally, many warehouse inventory teams rely on manual cycle counting to maintain inventory accuracy. However, this method is labor-intensive, time-consuming, and costly. Warehouse teams can also rely on excessive inventory as a safety stock which also can be a non-value-added cost.
Due to the high costs associated with production downtime, some manufacturing facilities resort to full facility counts when inventory accuracy falls below a certain level. One industrial engineer told us that, at the warehouse they support, they have to do physical counts when their accuracy falls below 95%. These counts require significant resources and cause the factory line to come to a halt until the physical count is completed.
Manual counts also don’t offer traceability and accountability and can be prone to human error. Supply chain, purchasing, and warehouse operations teams can’t see what’s actually in the warehouse, how it looks over time, and the history of where pallets have been stored.
Transforming Inventory Visibility with Gather AI
Our drone-powered inventory monitoring solution addresses the inventory challenge manufacturers face. Our drones autonomously navigate through a warehouse, capturing images of inventory locations - 15 times faster than traditional cycle counting. Leveraging advanced machine learning algorithms, our solution analyzes barcodes and text in the images, comparing them with the information stored in the WMS or ERP. We then display the results on a dashboard where inventory teams can see a list of matches, empty locations, and exceptions.
Inventory team members can then view pictures of the locations and exceptions and expedite their WMS reconciliation process from their desks and can quickly reconcile inventory errors, eliminating line-down and missed shipments.
The inventory team is also able to search for inventory by unique attributes such as lot or batch codes to see where and when the product was last located. Pallets are now traceable and teams can see the movement of pallets through a location and feel confident that the information in the WMS or ERP is accurate.
Because all of this information is available in the cloud, communications between supply chain, purchasing, and warehouse operations are streamlined. Everyone can access the same information from the same source of truth.
See how our solution works for one of our customers in this video.
Significant Benefits and Success Stories
Our customers have seen tremendous results from our solution. One warehouse reduced its full-facility inventory counting time from 90 days to just 2.5 days. For another customer, the solution has enhanced inventory accuracy by 70% in facilities that were already considered accurate, eliminating potential disruptions caused by inaccurate data. Additionally, the team has been able to reduce their MHE and reallocate and upskill cycle counters.
Conclusion
Inventory teams at manufacturing facilities rely on our cutting-edge solution to mitigate the risks of inaccurate inventory, eliminate costly disruptions, and streamline procurement. By leveraging the capabilities of drones and advanced machine learning algorithms, plant managers and inventory teams can achieve unprecedented levels of accuracy, improve operational efficiency, and boost revenue. Plant managers can feel confident that lines won’t go down because of poor inventory information and that distribution centers can ship product when it is needed. Embracing drone-powered inventory management not only transforms warehouse operations but also ensures a competitive edge.
Contact us to learn more.
Transform your warehouse.
No infrastructure changes necessary
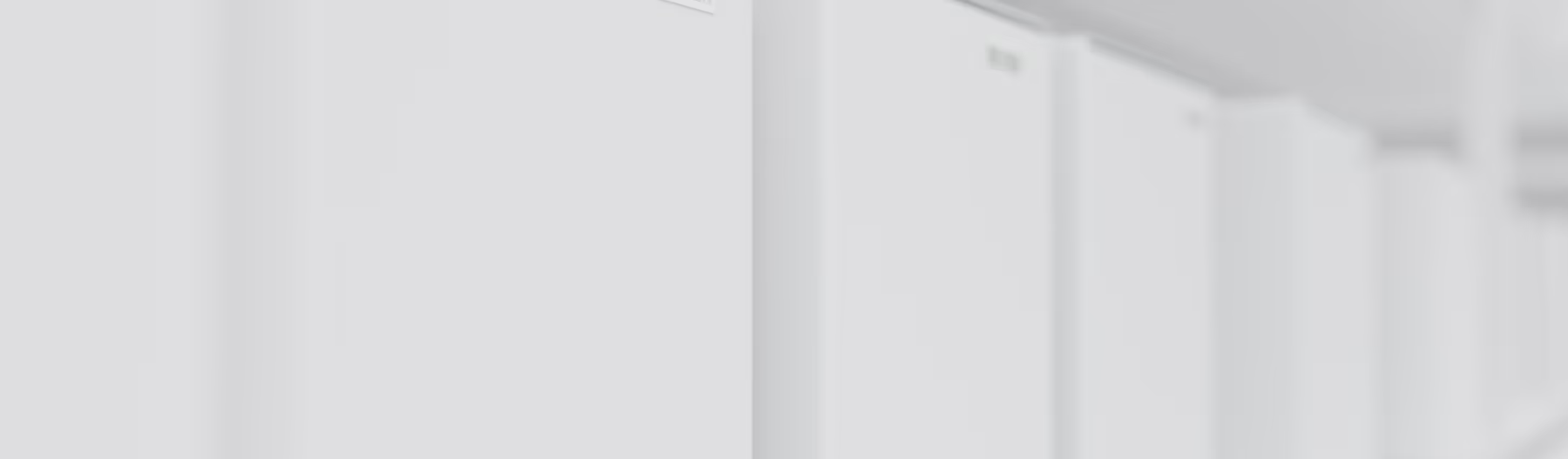