How to Harness AI to Combat the Eight Types of Manufacturing Waste
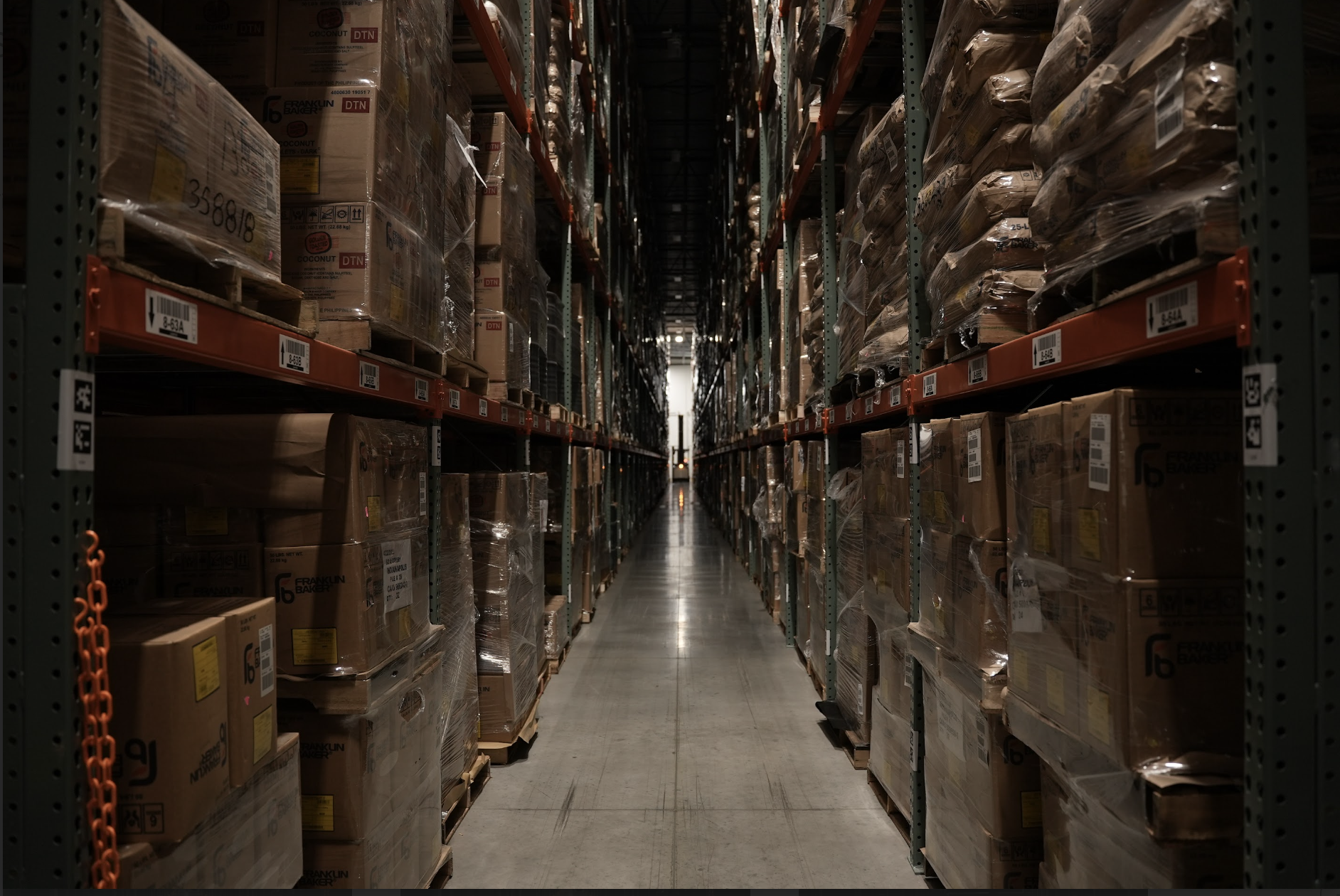
Let’s talk about what lean manufacturing looks like today. Some companies look to nearshoring and the elimination of shipping port congestion to operate more leanly. Others are evaluating their stock levels to produce just in time (JIT), without the risk of being too lean and having to halt production if they can’t find a single raw material. Importantly, digital natives are bringing new AI-based technologies to manufacturing facilities and warehouses.
So where did lean manufacturing begin? In 1950, Dr. William Edwards Deming consulted Japanese managers and engineers to improve their work internally, between departments, and externally, with their suppliers and customers. According to The W. Edwards Deming Institute® “Deming significantly contributed to the dramatic turnaround of post-war Japanese industry, and their rise to a world economic power. He is often called the ‘father of the third wave of the industrial revolution.’”
What is manufacturing waste?
In the 1980’s, Dr. Deming helped lead the resurgence of the American automobile industry, consulting with Ford, Toyota, Xerox, Ricoh, Sony and Procter & Gamble. These businesses drastically improved after adopting his methods. Deming pioneered concepts around lean manufacturing, and today The Lean Enterprise Institute and others use the acronym DOWNTIME to illustrate his philosophies and to define waste.
DOWNTIME encapsulates eight distinct categories of lean manufacturing waste. The acronym stands for defects, overproduction, waiting, non-utilized talent, transportation, inventory, motion, and excess processing.
By applying new AI-based technologies to your lean manufacturing line, you can manage these age-old waste types that still plague manufacturing plants and warehouses today. Let’s hone in on each type and talk about some ways AI can help.
8 Types of manufacturing waste
Defects:
This refers to production errors that require rework, repair, or result in subpar products. This waste can also mean products are stored in the wrong warehouse location due to mislabeling or misclassification and can lead to errors in order picking and shipping - requiring additional time and labor to correct the mistakes.
Companies can leverage computer vision AI to detect these defects at an exponential, more precise rate compared to humans. AI systems can also predict future failures based on the concept of a digital twin - meaning real-time data is being fed into a simulation model which is being continuously refined.
Overproduction:
Overproduction occurs when you produce more goods than needed or before they’re needed. If a warehouse produces or receives excess inventory that isn't immediately required, it leads to overstocking. This ties up capital and storage space and can result in products becoming obsolete.
By using various sensors such as lidar or computer vision, data can be transmitted to an AI system which gives you historical, current, and future stock levels of a specific SKU. This will ensure you match customer demand and don’t over or under-produce.
Another way to manage overproduction is to have very accurate inventory information. Some companies are using autonomous drones, including our solution, to improve inventory monitoring. Our software enables drones to fly autonomously through warehouses to photograph inventory stored in pallet locations. Our AI reads bar codes, text, and other information in the photographs and automatically compares it with what’s in the warehouse management system (WMS).
By using drones to do inventory monitoring, you can constantly monitor your finished goods inventory and ensure that you haven’t overproduced and have the right stock for shipping when you need it. Users of the solution report that they’re able to scan their full facility in two and a half days versus 90 days with traditional methods, ensuring increased inventory accuracy.
Waiting:
Waiting waste refers to production delays caused by idle time, equipment breakdowns, or inefficient processes. In manufacturing, this could be a down scenario, where production processes are being starved. Or if workers have to wait for a forklift to become available to move goods from one location to another, it creates downtime and hurts efficiency.
Data captured by AI-enabled cameras can result in accurate, live inventory location information, which eliminates shutting down the production line, reduces the need for excessive work in progress, and it can predict future line downs due to mechanical failures.
With drone-powered inventory monitoring, customers report improving their inventory accuracy by 70% as drones are able to count up to 900 locations per hour. High inventory accuracy means that raw materials are where they should be when they are needed for the line, eliminating line down.
Non utilized talent:
This involves not maximizing the skills, knowledge, and creative abilities of employees. If managers only use warehouse employees for manual labor and fail to engage them in process improvement discussions, it’s a missed opportunity for creative problem-solving and innovation.
AI frees folks up to do what humans are good at. Our drone-powered inventory monitoring solution frees employees up from doing manual inventory on forklifts and allows them to do more value-added activities like researching variances, auditing, and training to support operations.
One customer of the solution was able to reallocate five cycle counters. They are now able to use people for higher level tasks including continuous improvement initiatives and fixing errors as opposed to finding errors.
Transportation:
Transport waste occurs when materials or products are moved more than necessary within the production process. This can result from poor layout or disorganization, leading to extra handling and increasing the chances of damage and slowing down operations.
AI-based inventory monitoring technologies, including drones, can help employees find empty locations so there’s no wasted time driving forklifts around the warehouse. Also, accurate inventory reduces the number of ‘pallet emergencies’ which occur when a picker arrives at a location and the inventory is misplaced.
You can also lean on intelligent conveyance, automated guided vehicles (AMRs) and automated guide systems (AGS).
Inventory:
Inventory waste is the result of maintaining excess raw materials, work-in-progress, or finished goods. An example in the warehouse could be keeping large amounts of inventory on hand to meet potential demand, resulting in increased holding costs, including storage and insurance expenses.
AI and machine learning technologies can help manufacturing staff members see which pallets of product are expired. With our solution, vision-based drone-powered inventory monitoring, AI can read text in images taken by the drones and can output lot codes and expiration dates to a dashboard. When searching by lot code, you can find the locations where the product is stored, view images of the product at these locations, and ensure the product is available for the manufacturing line.
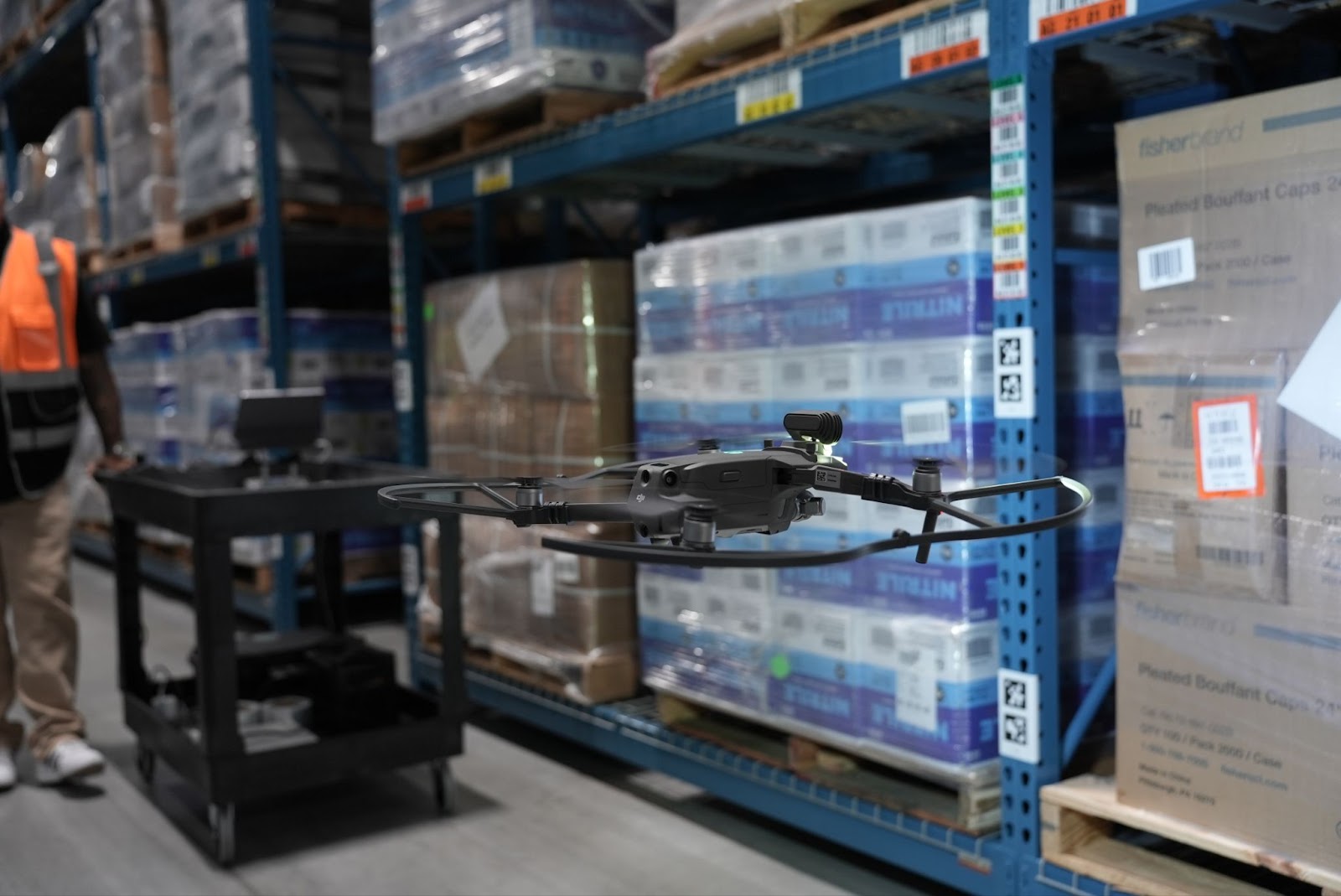
Motion:
Motion waste refers to any unnecessary physical movement of workers, such as bending, stretching, or walking. If an operator goes to a pick location that is inaccurate in their system, the operator will go on a search mission resulting in unnecessary movement.
Use AI to optimize task allocation and travel paths to ensure the closest available worker or robot is assigned the task of moving product from one part of the process to another.
With drone-powered inventory monitoring, one warehouse reallocated $250K of material handling equipment because it wasn’t needed for cycle counting. Another reduced pallet emergencies from 20-30 per day to one to two per day.
Excess Processing:
Extra processing waste involves performing additional, non-value-added steps that don’t improve product quality or function. Repeatedly checking, counting, or sorting products or materials due to inefficiencies in the initial processes can be considered extra processing, adding unnecessary labor and time.
Employees can use AI to gain access to real-time product feedback from the end users, perhaps through online reviews or customer service data. This will identify areas in your manufacturing process that can be removed, which saves time and money.
Conclusion
In a warehouse setting, reducing these wastes requires continuous improvement including optimizing processes, improving layouts, enhancing worker engagement, and using AI technologies to streamline operations. By addressing these wastes, warehouses can increase efficiency, reduce costs, improve quality, and better serve their customers.
About Gather AI Sales Director, Evan Rago: Evan Rago has over 15 years of experience helping manufacturing plants and warehouses optimize their material handling and inventory processes through innovative technologies. As a graduate of the University of Pittsburgh with a degree in Industrial Engineering, Evan is an expert in Lean/Six Sigma methodologies and has a track record of driving significant improvements in efficiency and productivity for his clients.
He currently serves as the Sales Director at Gather AI, a drone-powered inventory monitoring solution. He is responsible for driving revenue growth and expanding the company's customer base. Evan leverages his background in industrial engineering, emerging technologies, and supply chain expertise to educate folks on the benefits and applications of adopting warehousing drone technology.
Transform your warehouse.
No infrastructure changes necessary
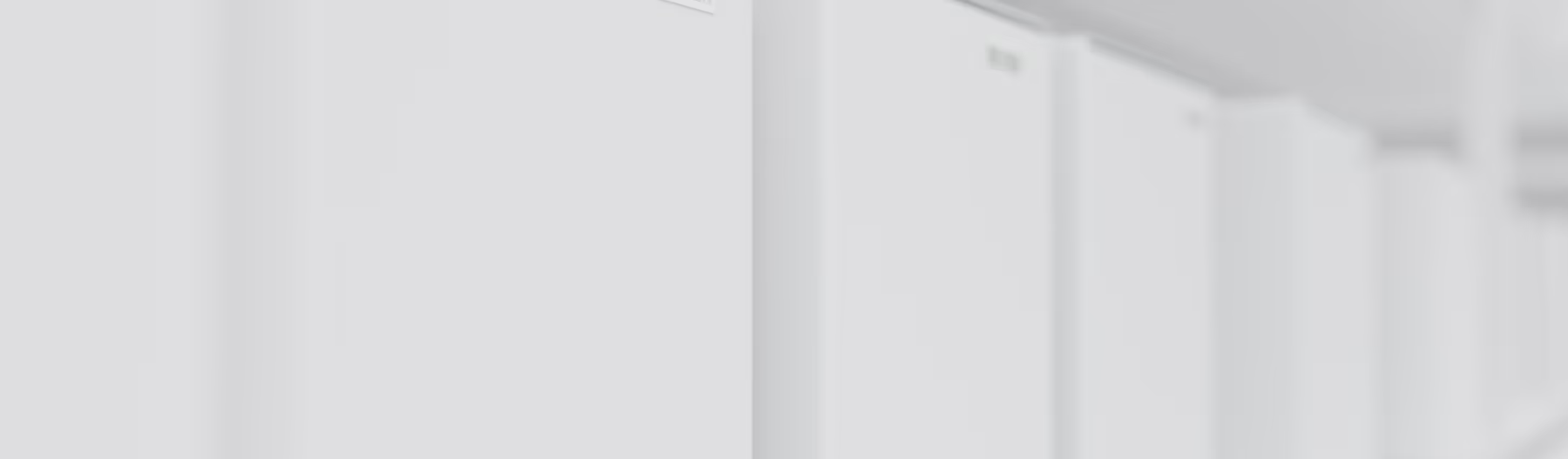