Types Of Warehouse Automation And Robotics
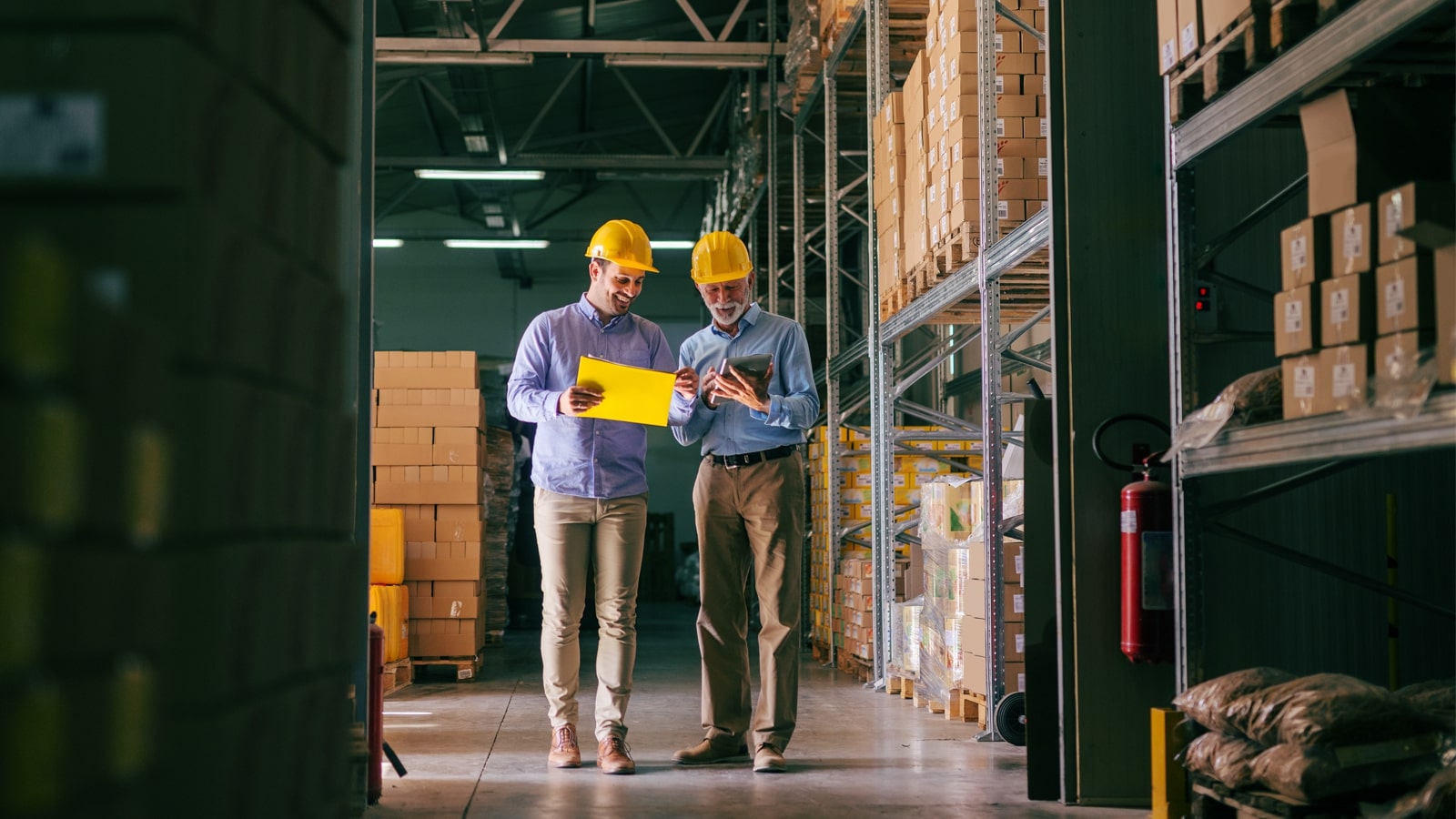
Warehouse automation has matured to the point that collaborative robots of all types are being deployed alongside their human counterparts to actively improve the throughput and operations of warehouses around the world. During the pandemic, shoppers have increasingly turned to e-commerce as a safer alternative to shopping in-store. The result is that quarter after quarter, new records are being set for e-commerce sales. This in turn puts increasing pressure on distribution centers, fulfillment warehouses and the logistics operations for the supply chain.
The Goals of Warehouse Automation
Picking and packing products for customer orders all day can be dangerous, difficult and exhausting work. Every warehouse manager knows the struggle to hire and retain a human workforce, due in part to these high pace working conditions.
The first goal of automation is to improve warehouse processes by automating much of the repetitive process workflow. The second goal of automation is to remove people from dangerous processes that can cause injury. This enables people to move to work that is of higher value.
The third goal of automation is to improve order accuracy and shorten fulfillment cycle times through the scanning of product SKU’s and tracking of inventory at every step of the fulfillment process. Automation can also be measurable and predictable, enabling optimization through the elimination of bottlenecks in your process.
The fourth goal of automation is to increase operational flexibility and agility. Automation reduces the dependency on people to do operationally critical tasks. Lastly, when you automate repetitive processes like palletizing, or the movement of bulk inventory, you eliminate the opportunity for injuries and make the work less tiring for your human workforce.
History of Warehouse Automation
Historically manufacturing has led the charge in adopting autonomous technology such as AGVs. Automation was limited in warehouses because of the dynamic nature of warehouse operations. Warehouse used classic “hard” automation in the form of fixed conveyors, and automated sortation & queuing systems. Hard automation is designed to improve the throughput for linear workflows that are measured by throughput volume and accuracy.
Flexible automation helps to future-proof a warehouse by enabling quicker reprogramming of a process to adjust to changes in demand or to take up the slack during peak periods. Today, these flexible and automated workflows included robotic arms deployed to pack boxes with products and then palletize these boxes onto shipping pallets. In the 2010s, smart carts and autonomous mobile robots (AMRs) began to be deployed in warehouses to help move products through the warehouse. Along the way, these AMRs have replaced manual carts and fixed conveyors, while helping improve the efficiency, flexibility, and material flow throughout the entire warehouse.
Types Of Automation Workflows
Today, robotic automation touches every workflow process in a warehouse, from the time products are received on the shipping dock, put-away, inventoried, picked, consolidated, and finally shipped out the dock door. There is a robotic based solution for every step of the warehouse fulfillment process.
Typical Fulfillment Workflow:
- Receive bulk product on loading dock
- Audit and label incoming product at staging lanes
- Put away inventory
- Pull item(s) for a customer order
- Consolidate customer order
- Label & postage
- Sort by carrier/destination
- Consolidate orders
- Ship
- Reconcile inventory
Collaborative Robots Work With Humans
Robotics evolved over the last two decades to become collaborative with humans. A collaborative robotic system is one that can safely work beside humans. Some robotic applications, such as robotic palletizers, or inventory storage solutions, still need to operate behind safety fences. However, there are now collaborative robots (cobots) that can safely work in the same workspace as their human counterparts. Autonomous mobile robots come in many forms, from autonomous carts for piece picking in a person-to-goods operation to autonomous pallet trucks that can acquire and move heavy pallets around the warehouse. Even the airspace in the warehouse is now being filled with autonomous drones capable of safely navigating the warehouse to perform autonomous inventory tracking.
Artificial Intelligence Opens New Opportunities For Automation
Artificial intelligence has evolved such that these solutions can now learn from their environment and become smarter and more valuable over time. Computer processing hardware has also become miniaturized and able to consume less power, thanks in part to the maturity of mobile cellphone technology.
In the last decade, drones have progressed from difficult-to-fly, line-of-sight, hobbyist platforms into vision-guided, fully autonomous aerial robots. Commercial drones are now robust enough to be deployed in industrial inspection use cases.
In the warehouse, a viable application of an autonomous drone is to perform inventory counting. An aerial drone can fly a mission through the warehouse and take pictures of each inventory storage location. Unlike a ground-based mobile robot, a drone can fly up and take a picture of a pallet stored at any height. As the images are processed, artificial intelligence can assess the image, read a barcode or text and detect empty locations. This information can then be immediately reconciled into the warehouse management system, updating the inventory in real time and making the entire fulfillment process more efficient.
Warehouse Automation is the Future
Automation is indeed at the maturity level that it can be integrated into your warehouse workflow and provide immediate impact to your bottom line. These solutions are collaborative and have the ability to work together with your human workforce to improve the efficiency and throughput of your warehouse.
Transform your warehouse.
No infrastructure changes necessary
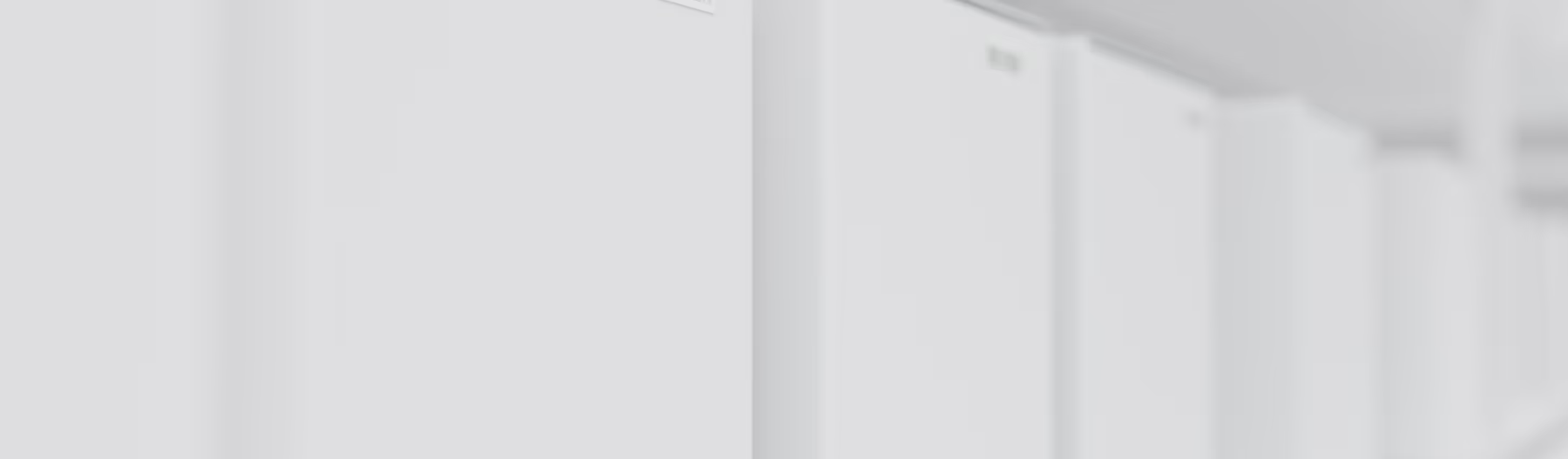