5 Benefits of Warehouse Automation
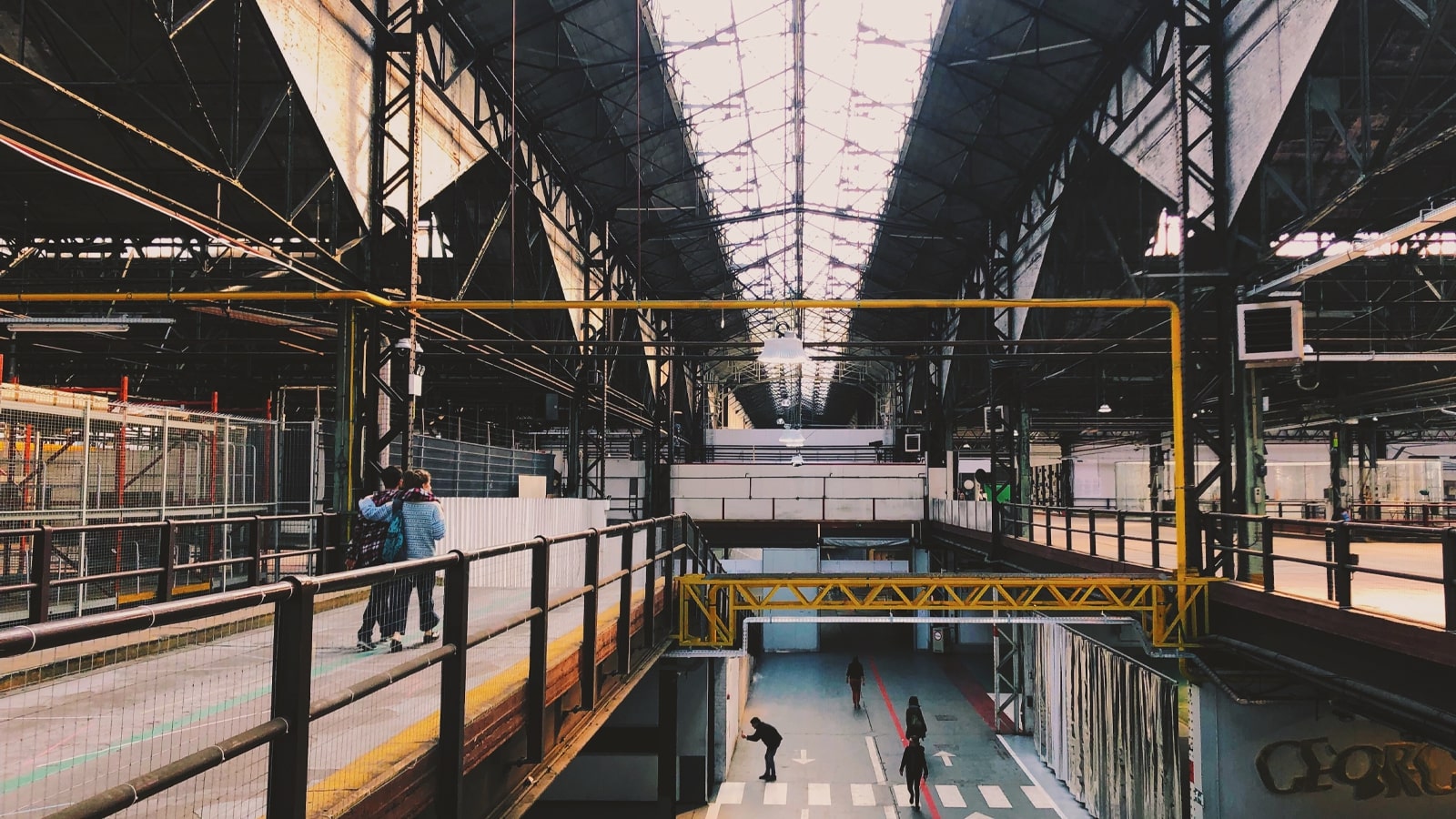
Technology is changing the warehousing landscape, with operators integrating cutting-edge equipment, systems, and solutions. Warehouse automation technologies such as goods-to-person, automatic guided vehicles, warehouse drones, and sortation systems enable operators to streamline processes, operate more efficiently, improve safety, and more.
Automation is one of the leading trends in the industry. Recent figures show that the global warehouse automation market will be worth $51 billion by 2030, with the worldwide pandemic turning warehouse automation technology from a “good to have” to a “must have.” Furthermore, a 2021 McKinsey survey found that 80% of respondents plan to increase automation spending in the next two to three years.
We’ve outlined five factors your warehouse could benefit from by adding automation:
1. Optimize labor utilization
The U.S. labor market has proven resilient in recent years, resulting in rising wages and few layoffs, and labor shortages have been compounded by the fallout from COVID-19. We’re in a buyer’s market for sure. Hiring the volume and caliber of talent you need can feel like an uphill battle. Warehouses and distribution centers are hiring hundreds of employees at job fairs knowing more than half won’t show up on their first day.
In warehousing, staff is thin on the ground, and can be expensive. Employers understand that, and it’s right that highly skilled people are well compensated. It doesn’t make sense to assign them to roles that can be easily carried out by automated warehousing technology. Automating everyday warehouse tasks like inventory tracking or order picking allows you to allocate human resources to other more valuable or important tasks.
This is something you can benefit from almost immediately. And in this highly competitive labor market, it’s a great example of how warehouse automation can be used to keep your staff engaged and motivated.
2. Increased efficiency
Efficiency is a word we often hear, and it can mean slightly different things depending on the sector you work in. But in warehousing, efficiency means finding a way to make things easier. Warehouse operators must ensure their high-value inventory isn’t in a dark corner of the warehouse when there’s space near the delivery/drop-off area, for example.
The most efficient operations, whether in warehousing or elsewhere, are those with the most up-to-date and accurate information. Automation can collect and deliver actionable data quickly while eliminating the problems associated with inaccurate reporting. With reliable data, warehouse operators can carry out vital tasks such as order fulfillment, stock replenishment, and inventory management confidently and efficiently.
Automation in the warehouse can also create efficiencies by doing repetitive jobs, such as picking and stacking faster than manual operatives. Additionally, software and AI can pinpoint inefficiencies in warehouse operations. For example, when tasks are taking longer than expected - allowing changes to be made to boost operational efficiency and productivity.
3. Improved safety
One of the very best benefits of warehouse automation is improved worker safety. There is technology available now where you don’t need to send people 30 or 40 feet in the air on scissor lifts to count inventory or perform the same tasks hundreds of times a day.
Warehouse automation is increasingly being used to take on physically demanding and often dangerous tasks, such as inventory counting or checks at height. Machinery is being built with automation capabilities, flagging risks to human operators, and making them more aware of safety concerns. Automated technologies have also been designed to perform repetitive tasks, reducing the risk of employees being injured and picking up repetitive strain issues.
Using safety funding to replace risky tasks performed by humans with warehouse automation is money well spent. And it’s not just the human damage to consider. An incident at one of your warehouses could lead to significant reputational damage and possible legal action. Incidents can also shut down operations, leading to penalties for failing to fulfill orders.
4. Optimize space utilization
Saving space, or using it better, is essential for warehouse inventory management. A minor improvement in space utilization can help a warehouse become a leaner and more efficient operation. An organized facility is easier for workers to navigate daily and reduces the time it takes to fulfill orders. Part of that process is ensuring your cube utilization is high or, in other words, you’re using the space available to you smartly.
Automated warehouses can use up to 40% less floor space compared with traditional warehouses because automated technologies such as lifts, robotics, and drones can function in smaller spaces or harder-to-reach areas. This helps operators maximize their floor and vertical space (which can sometimes be underutilized).
5. Lower equipment costs
The cost of warehouse automation is often considered a barrier to entry for warehouse automation, especially for small to medium-sized companies. Investing in warehouse automation can actually lower equipment costs and provide fast ROI.
By adding automation, warehouse operators can phase out older machinery that can often cost tens of thousands of dollars to purchase and maintain. Automated technology has the potential to replace manual equipment in several areas of the warehouse, including production lines, picking and stacking, inventory, and packaging. In addition, traditional equipment commonly has to be operated by trained - and often expensive - personnel, whereas warehouse automation technology requires significantly less human oversight.
Transform your warehouse.
No infrastructure changes necessary
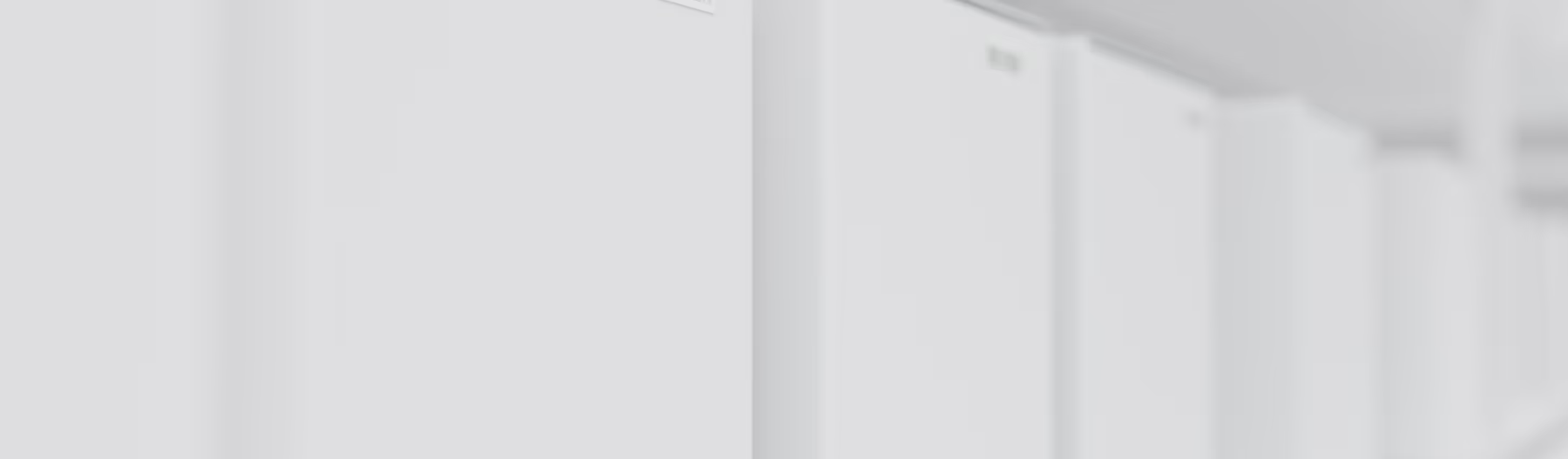